They Ask- We Answer
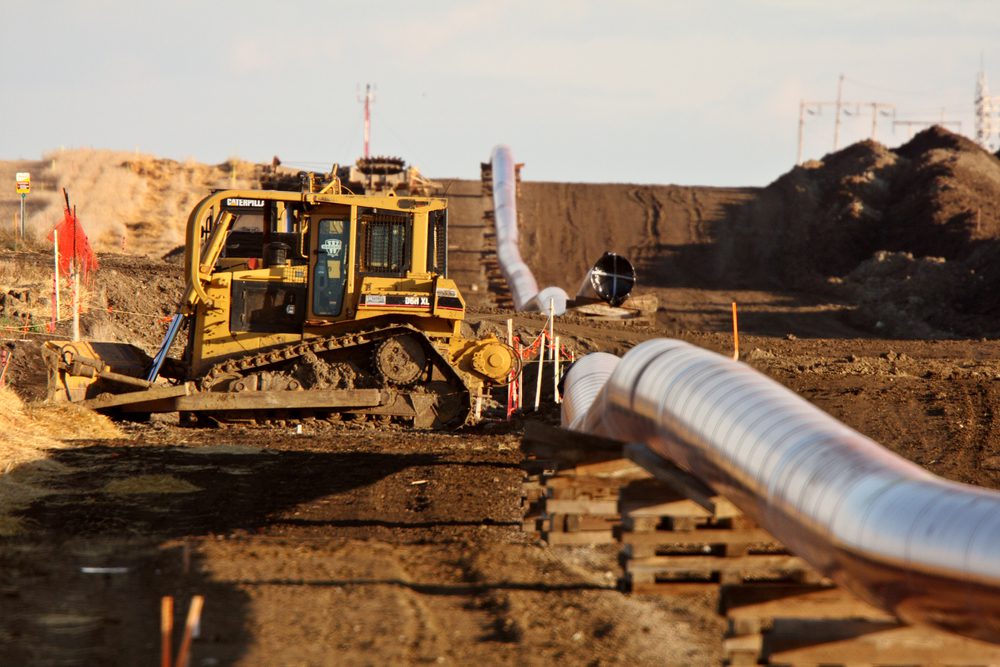
Why is Engineering so expensive?
The illustration on the Pricing Tab provides a guideline for Engineering Costs. Engineering is expensive because to sacrifice the level of skilled and experienced people, the multi-discipline environment we maintain, the software packages we utilize, the certifications and insurances we maintain will cost your project much much more and will put you and your company at risk if this level of design rigour is compromised.
Can Engineering Costs be reduced?
Engineering costs are best reduced by:
1. Rolling a client’s EPCM team from project to project to leverage on field personnel relationships and supplier relationships to continually minimize the learning curve.
2. Try to standardize and template equipment and designs as much as possible.
3. Minimize changes once the project frame has been established.
4. Embrace the input from field personnel early and often. All too often this valuable input is engaged too late or not at all.
Does it make sense to try to minimize Engineering costs?
There is always a balance to find in Engineering Cost versus total project cost. There is a rule of thumb to ” spend $1 in the office will save you $10 in the field” and there are times where this is very true. But there are also times where larger engineering firms will bury hours of non-essential personnel into project invoices. Finding this balance is critical because a “rising tide lifts all boats” meaning that successful projects attract capital to invest in more projects and conversely unsuccessful projects scare capital away to other jurisdictions or other industries.
Why do I need Engineering at all?
Why can’t I send my trusted field guy out to site and put this together and save this engineering cost? If this can be accomplished what VALUE does engineering bring?
This strategy can work some of the time. For the times that it does not work will cover the costs of proper engineering on all projects. The upside of this proper engineering will be improved reliability, scalability, standardization and simply the intangible benefit of you being able to sleep at night. There is no cost benefit over a program of projects to expose yourself and your management/ directors to this short cut. Over the program of multiple projects the engineering services will pay for itself may times over.
How can I reduce my overall project costs?
The best way to minimize project costs are:
1. Engage field personnel early and often.
2. Approach projects with the philosophy to minimize field time. This means prefabricating as mush as possible in a shop environment with accurate drawings and hopefully bid the work as this implicitly forces a scope freeze.
3. Minimize changes once the process design of the project has been agreed to. The “tail cannot wag the dog” meaning that the business case can and will dictate changes over the project life cycle but changes must be aggressively evaluated and pragmatically implemented by experienced people so as to not upset the overall design process.
4. Minimize the changing out of project people.
5. Maintain a smooth and orderly execution. Minimize overtime and working off adrenaline as this over time causes mistakes and causes project staff turnover.
Cost Estimating
Cost estimating is one the most important aspects of any successful project. If the initial estimate is not accurate and is priced too high, the project may be deemed uneconomic and resources reallocated to more viable projects. If a project makes it past the vetting phase, the estimate continues to evolve throughout the lifecycle of the project as assumptions are verified.
Tundra’s vast and recent project experience provides us with an extensive database of costs to leverage for new projects. One of the best ways to forecast future projects is to use relevant information from past projects. Having access to this information allows Tundra to provide relatively accurate cost estimates at the early stages of a project.
Every business uses their own interpretation of the various classifications of cost estimates, but the following stages of cost estimating fall within the industry accepted ranges:
- Class V: -50% to + 100%
- Conceptual phase. This estimate is used for project viability and, sometimes, a comparison between several different options to determine various return on investments.
- Very little scope definition is available at this stage.
- Class IV:-20% to + 30%
- Design Basis Memorandum (DBM) phase. This estimate usually accompanies the DBM and defines a number of variables for the project. No other options are being evaluated at this stage as they have been vetted through the Class V estimate(s).
- More scope definition is available. Usually a preliminary Plot Plan, Process Flow Diagrams (PFDs) and a Single Line Diagram have been created.
- Class III: -15% to + 20%
- Front End Engineering and Design (FEED) phase. This estimate is generated as the result of detailed engineering design.
- Scope has been clearly defined. Detailed drawings such as Isometrics, Pile Layouts and Electrical Layouts have been generated. An Authoriziation for Expenditure (AFE) is created based on this level of estimate.
- Class II:-10% to + 15%
- Bid tender phase. This estimate is based on costs incurred to date and the return of all bids packages from vendors and contractors.
- Scope is finalized and all engineering design deliverables are complete. AFE costs are verified based on this level of estimate.
- Class I:-5% to 10%
- Final cost check phase. This estimate is based that a majority of costs that have been incurred to date.
- All major equipment has been delivered with most of the fabrication work now complete. Refinement to the estimate is typically only required for certain sections of the project that may have been deemed higher risk. AFE costs are once again verified and trends are developed to predict over or underruns.